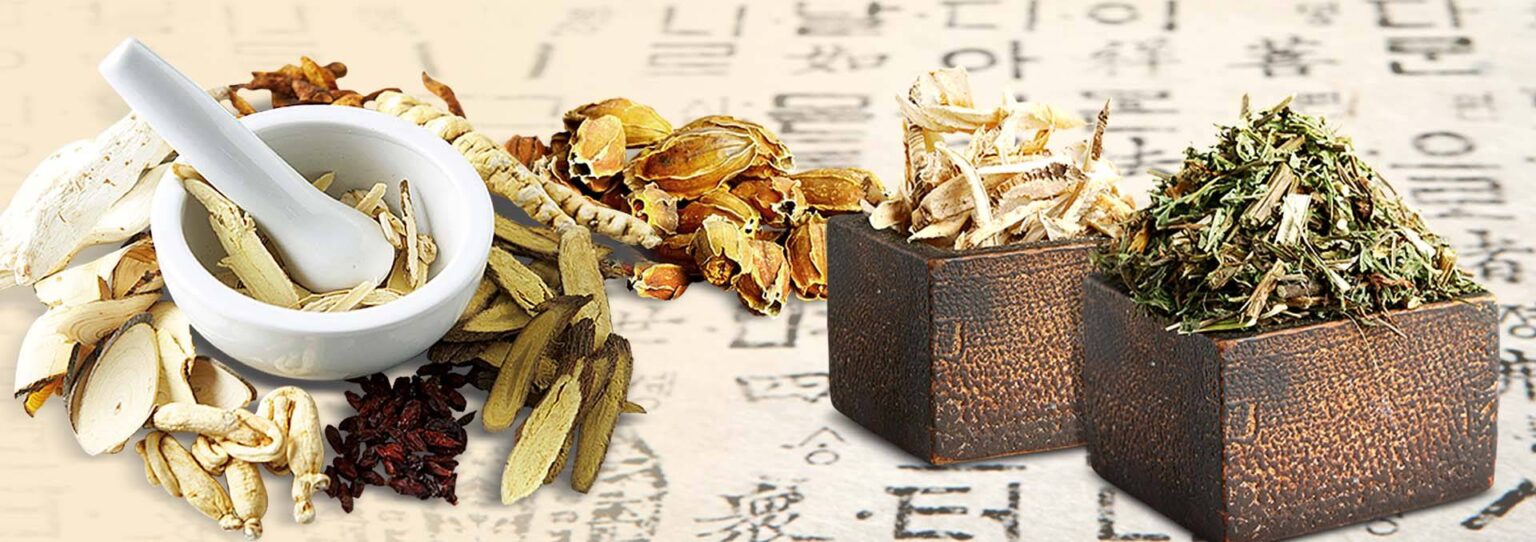
The Kampo Product Manufacturing Process
Unpacking and Sorting
Raw Materials for Crude Drug that are delivered to Shenzhen Tsumura Medicine Co., Ltd. in China or to the Ishioka Processing & Quality Control Center in Japan are sorted both by hand and machine before being stored in a low-temperature warehouse.
During storage, crude drugs are sampled according to specified procedures, and are checked for macroscopic and microscopic appearance, as well as the content of each botanical extract and marker components by physicochemical testing. These tests are performed to determine whether their quality meets Tsumura’s standards for Kampo products.
At the warehouse, the crude drugs are identified by a location management system that utilizes ID cards with barcodes containing information on traceability. The storage of crude drugs is strictly regulated at a warehouse with low temperature (15 degrees Celsius) and low humidity (below 60%).
All raw materials for crude drug that are unpacked at Shenzhen Tsumura Medicine Co., Ltd. or at the Ishioka Processing & Quality Control Center are screened according to Tsumura’s in-house standards.
Cutting and Mixing
Cutting and mixing of raw materials for crude drug take place in the production rooms located on the 1st to 4th floors of the extract powder production building of the Ibaraki Plant. The crude drugs are checked for authenticity, batch number, and quantity before they are cut into particle size for maximum extraction with a cutting machine tailored to each botanical type.
The amount of materials that is cut is based on the unit quantity of Kampo formulation for production. Once cut, they are used immediately to prevent any deterioration in quality.
Cut materials are weighed and mixed according to the prescribed mixing ratio, and then transferred to large stainless-steel containers. The unit quantity for mixing is approximately 500 kilograms.
Process of Extract Powders
Extract powders are manufactured in the production rooms on the 1st to 4th floors of the extract powder production building of the Ibaraki Plant.
The manufacturing process of extract powder includes extraction, solid-liquid separation, concentration, and spray drying.
Tsumura uses proprietary extraction vessels and purified water to perform hot water extraction (decoction) of raw materials for crude drug. This is to ensure equivalence in quality and quantity between the extract powder and standard decoction.
A continuous centrifugal is used to separate the liquid extract from the residues of crude drugs. Low-temperature vacuum concentration of the liquid extract with a continuous film evaporator reduces concentration time and prevents a loss of bioactive constituents.
Tsumura’s proprietary spray-drying device instantly dries and cools the liquid extract into high-quality, dry extract powder.
The concentrated liquid that is sprayed from the top of the dryer is analogous to spraying the liquid from the top of a four-story building. This process helps minimize thermal influence on the extract powder.
Granulation
Granulation is performed on the 1st to 3rd floors of the three-story granulation building located at the front of the Ibaraki Plant. Extract powders manufactured at Shanghai Tsumura Pharmaceuticals Co., Ltd. are made into granules at the Ibaraki Plant.
The granulation process includes sieving/weighing, mixing, blending, and granulation.
The extract powder, lactose, and other excipients are sieved until their particle sizes are constant, and are then weighed and mixed according to the prescribed mixing ratio of each formulation.
A large machine is used to thoroughly mix the extract powder with lactose and other excipients.
The mixed powder is compressed into tablets before they are crushed. A classifier is used to separate the granules into uneven, small, or product-grade, with only product-grade granules selected for the final product.
Filling, Packaging, and Release
Filling and packaging are performed on the 1st to 3rd floors of the production room adjacent to the granulation building of the Ibaraki Plant.
Extract granules are packaged in aluminum sachets with a machine that can at once fill 12 sachets per sheet and also simultaneously and automatically weigh each sheet.
The automatic sachet machine stitches three sachets together and binds seven sheets of three-sachet packets as one batch. A total of nine batches are boxed in the same container by a robot. The final products are placed into cardboard boxes and stored at the automated product warehouse before they are delivered to two logistics centers located in East and West Japan.
All processes at the logistics center are fully automated and computerized to eliminate any error in release, and to ensure the timely release of products in response to customer orders.